A successful shift to a circular economy requires multidisciplinary skillsets that integrate both business and technology aspects. However, circular economy or sustainability practices are not often seen as competitive advantages for companies. The ConnectedFactories project focussed on devising potential pathways to digital manufacturing, including circular economy from a broader perspective.
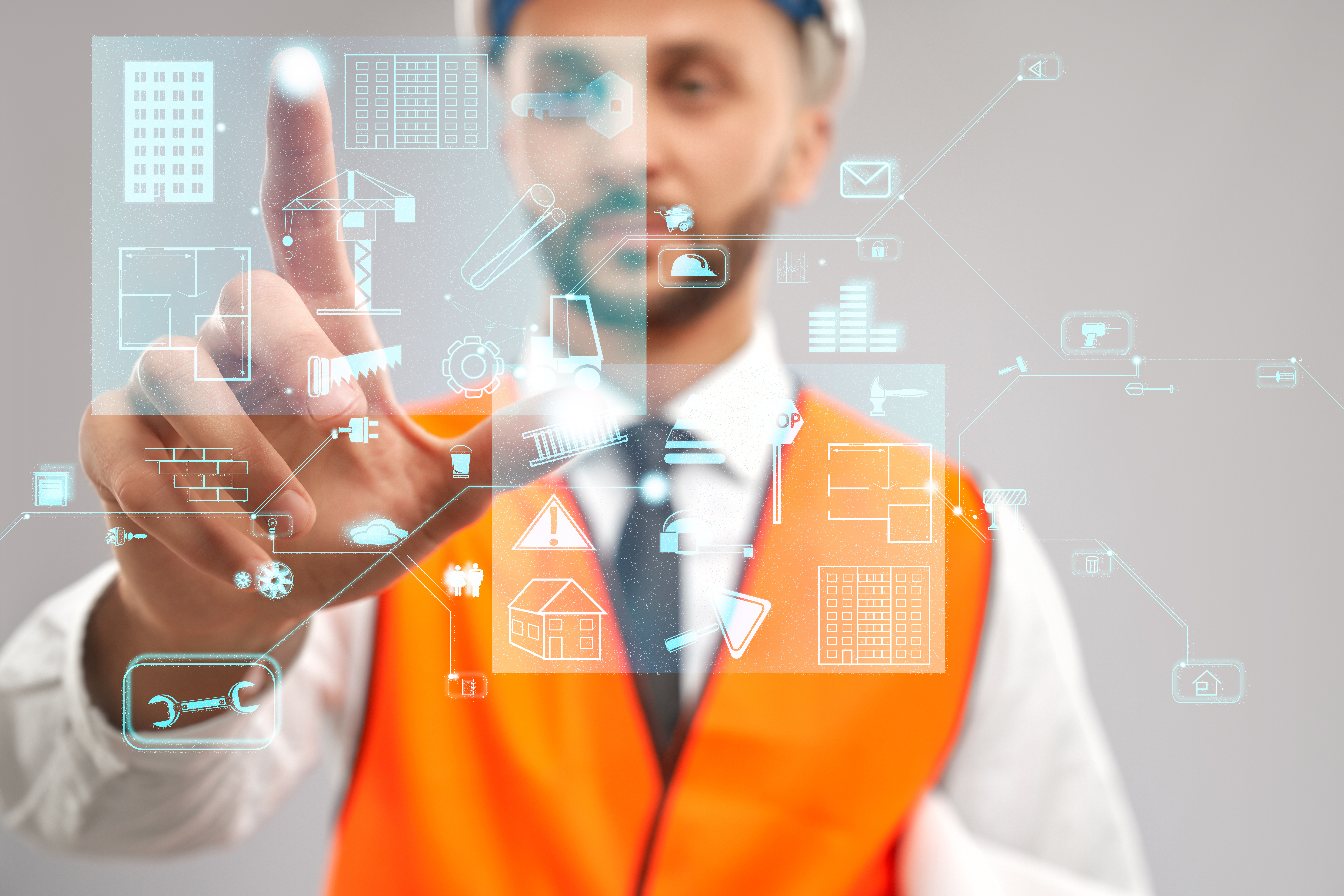
The ConnectedFactories project investigated how manufacturing systems and processes can become digitally integrated and work seamlessly together. It uncovered crucial factors and tools that can make this integration possible. In addition, ConnectedFactories connected different projects and their outcomes, practical examples, and demonstrations to the strategies and important factors identified. The project has been initiated by EFFRA, the European Factories of the Future Research Association.
The ConnectedFactories consortium also figured out what factories need now and in the future, as well as the problems they might face across different pathways and the importance of cross-cutting factors, such as interoperability or legal aspects. It was a project composed of two phases, namely Connected Factories 1 (running from 2016-2019) and Connected Factories 2 (2019-2021). The first project focussed on three pathways, namely smart autonomous factories, hyperconnected factories, and collaborative product-service factories. The second project added pathways on circular economy, cybersecurity, data spaces, and AI.
“In the first level of the smart autonomous pathway, for example, many companies utilise spreadsheets for data management. But to optimise data gathering and processing practices, one needs more advanced solutions and dedicated software platforms,” says Chris Decubber, who coordinated the first effort of the project and supported Connected Factories 2. “As soon as companies can establish more dedicated data processing, they can use that data to improve their manufacturing processes, in some cases even consider automated interaction between the data analytics side and the actual operation of the processes supported by real-time decision making.” These pathways thus describe the structured progression toward achieving advanced levels of digitalisation of manufacturing.
Among the pathways explored, the Circular Economy pathway was devised to emphasise the importance of circularity for sustainable manufacturing, encouraging companies to embrace this approach. However, often, SMEs find it difficult to invest in new circular approaches and supporting technologies while focussing on growing their business through finding new customers, partners and developing new products. “You clearly have a lot of inspiring approaches and technologies out there, but if nobody knows about them or knows how to use them, then there is no point,” says Decubber. “Additionally, if the management does not have a clear insight in the economic viability and a clear indication that these technologies will make a difference, they won’t be introduced, regardless of whether operators know how to use them or not. And that is also an important aspect to be considered.”
ConnectedFactories developed a pathway to help companies understand where companies stand in relation to the Circular Economy and where they can improve. It assesses different aspects of their business and compares their position to an ideal one and to other companies on the same journey. Companies don't have to follow a strict, step-by-step process to reach the ideal state, but rather, the path to improvement can be flexible, especially for newcomers.
The CE pathway starts with companies operating in a linear manner, where they meet environmental regulations but do not view CE and sustainability as strategic advantages (level 1). Many companies then move on to piloting initiatives to reduce energy and material inputs, often driven by a desire to enhance their brand image (level 2).
A significant step towards more sustainable manufacturing involves systemic resource management, where data from various sources is used systematically to improve resource efficiency and circularity (level 3). Moving to the next level of CE thinking, companies collaborate with their value chains to explore environmental, social, and economic sustainability aspects. This network-level activity is crucial for fully embracing the Circular Economy (level 4). The most advanced phase is ideal circularity, where companies and their value chains are restructured to create closed or cross-sectoral value loops. In this phase, data flows and data spaces play a crucial role in highlighting the positive sustainability impacts (level 5).
This pathway has clear implications for the kinds of skill sets required to fulfil it, and the cross-cutting factors on human skills demonstrate this. From linearity, which demands simple tasks such as recycling and other environmental obligations, more strategic thinking is found in subsequent levels. Strategies aiming towards resource sufficiency, such as disassembly, require a product lifecycle manager to look at the whole supply chain, rather than just the product. More advanced levels would incorporate servitisation, thereby focusing on the customer service experience to help customers choose resource-efficient options, and industrial symbiosis to maximise exchange of resources and materials across industrial actors.
Walking through an example that illustrates the challenges of circularity in the (re--manufacturing context, Decubber considers the manufacturing of electric motors. “While there are ongoing advancements in disassembling, reusing, and recycling them, a crucial question arises: how do we handle the disassembly process, and can automation play a role in it? When we're dealing with thousands of engines being repurposed for a second life, it's likely that a combination of manual labour and automation will be necessary. However, this raises another important question: were these engines originally designed with disassembly in mind? In this scenario, the entire maintenance or remanufacturing process must undergo a comprehensive redesign. We need to determine which tasks can be automated and which ones require human intervention, all while ensuring that the engines are designed to facilitate the disassembly process effectively.”
The challenge boils down to the product itself, as often the products that are being put on the market were not originally designed for disassembly. SMEs will therefore have to assess the entire product value chain to understand the critical processes and skill requirements needed to be on the path headed towards a circular economy.